The European Union is embarking on the transition to a climate neutral economy with the blueprint laid out in the European Green deal. The European Green deal will have an unprecedented impact on all industries across Europe and the globe, not least of all the polyurethane sector. By 2050, The European Union aims at becoming a sustainable and climate neutral economy, while already reducing greenhouse gas emissions by 55% by 2030. The European Green Deal includes major action fields mobilising the polyurethane industry for a clean and circular economy.
The next challenge is how to turn the Green Deal blueprint into reality. It is an immense undertaking and the inherent properties of polyurethanes provide sustainable solutions to address many of the challenges of the Green Deal. An important aspect of the Green Deal is moving from a linear model towards a circular economy. The circular economy is a model of production and consumption, which involves sharing, leasing, reusing, repairing, refurbishing and recycling existing materials and products as long as possible. In this way, the life cycle of products is extended.
To deliver on these ambitions by 2050, the polyurethane industry has launched a series of initiatives including the use of recycled resources and the development of recycling technologies to minimize waste and reduce CO2 emissions.
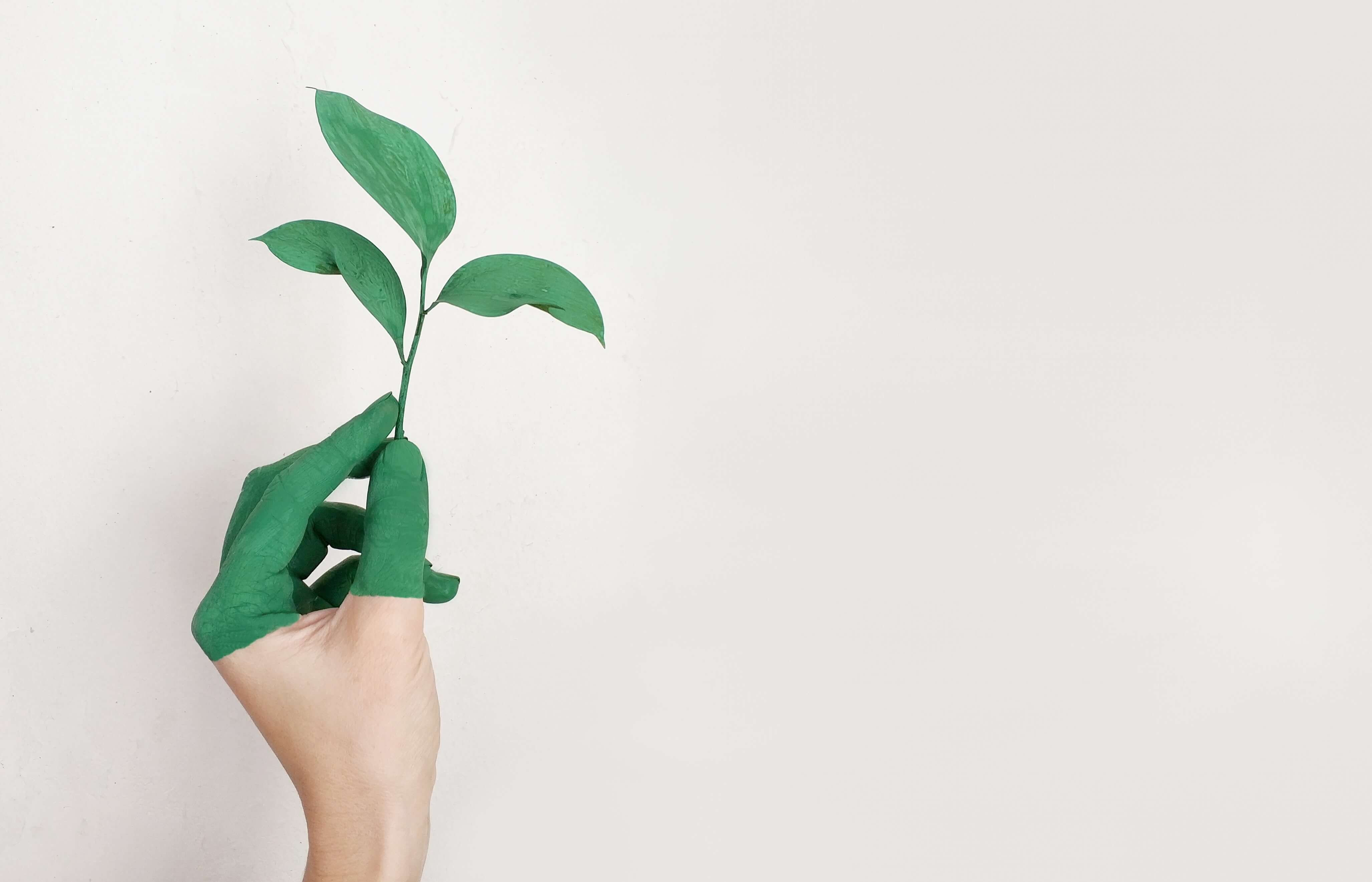
Polyurethane foam is a thermoset polymer. Contrary to thermoplastics, thermoset plastics are capable of becoming fully rigid when heated or cured. Because of its lightweight and unique properties, polyurethane foam is used in a variety of applications.
It can be tailored to be either rigid or flexible, with a market share of about 50:50. Around 90% of flexible PU foam is used in bedding, upholstery and automotive industry. The rest is used in a variety of applications, such as kitchen sponges, shoe insoles or as acoustic insulation, among hundreds of other applications.
PU rigid foam is a premium engineered insulation material used in a wide range of building and technical applications. Thanks to its low thermal conductivity and high durability, it may save more than 100 times the energy needed for its production during its 50-year lifetime – possibly more – in buildings.
Polyurethane foam is a durable material, normally made to last for the whole lifetime of the product that contains it. When PU reaches its End-of-Life phase – after many decades in use – it enters the waste stream, ready to be re-used or recycled.
Recycling Technologies
When it comes to the end-of-life phase of thermosets – contrary to thermoplastics – the recycling technology of heating or melting cannot be applied. Still, the polyurethane foam industry at large has been working at addressing this challenge over the past years. Many of the past issues have been resolved in the supply chain, the regulatory environment has evolved and recycling technologies have come a long way.
Today there are two main technologies available for the recycling of PU foam efficiently, mechanical and chemical (advanced / enhanced) recycling. The difference between the two is that chemical recycling follows degradation principle – meaning that polyurethane wastes are depolymerized into its primary raw materials.
Mechanical Recycling
Mechanical recycling as a method exists for decades. The PU foam supply chain has made great efforts already over the past decades to improve its resource efficiency at the production stage. Mechanical processing with or without the addition of binder is the easiest and most basic way to recycle PU. Today, almost all PU foam production and conversion waste or scrap is sold by foamers and converters as trim and to produce PU bonded foam used in various products.
PU foam found in comfort applications has the same lifespan as the product itself – up to several decades. On the other hand, the main application of rigid PU foam – sandwich panels – have a much longer average lifespan. This discrepancy results in different quality of mechanically recycled PU foam.
Chemical Recycling
Chemical recycling, also known as enhanced recycling, involves any type of reprocessing technology using chemical agents or processes that directly affect either the formulation of the plastic or the polymer itself. In this process polyurethane foam is broken down into chemical raw materials, namely polyols and diisocyanates. Considering costs, applied temperature and additional substrates, enhanced recycling is much more demanding than the mechanical recycling pathway.
There are two main chemical recycling technologies. The first one is chemolysis which is split in many different subcategories such as acidolysis, hydrolysis, aminolysis or alcoholysis, depending on the chemical reagents used. Today it is possible to recycle the polyols fraction of the PU foam with this technology, and research is taking place to also recycle the diisocyanates in the future. The second technology is thermochemical recycling, in which materials are brought back to a molecular level in oils and gases, which can be used as new raw materials for the petrochemical industry. Using the so-called “mass balance approach”, up to 100% of bio-based and/or recycled polyols and isocyanates could be used in foam formulations in the future.
Other Technologies
One technology more commonly used for recycling of rigid PU foam is biodegradation. This technology is characterized by the breakdown of organic substances by living organisms or their enzymes. It results in shortening of polymer chains and the elimination of some of its parts. That leads to the reduction of its molecular weight, and in favourable conditions, it can even result in the complete mineralization of degraded material. However, the complete degradation of larger polymers usually requires the cooperation of several different organisms. It can consist of a few stages: breakdown of the polymer to monomers, their reduction to simpler compounds and final degradation to carbon dioxide, water and methane (under anaerobic conditions).
Outlook into the Future
By some estimations, around 40 million mattresses reach End-of-life stage in Europe each year. For illustration, if they were all stacked up, the height would be equal 904 Mount Everest’s – the highest mountain in the world. The End-of-Life stage is critical for the rigid PU used in the construction sector as well. This is pushing the industry to team up with the academic world and legislators for innovation and the creation of new opportunities in the management of construction and demolition waste. While a lot of effort across the industry has been made to improve the sustainability of polyurethanes, we realize this is rather a marathon than a sprint.
Below is the overview of the remaining challenges the PU industry is working to solve:
- Getting access to the resource at local level,
- Designing for cost-efficient dismantling,
- Creating a market for recyclates,
- Creating the conditions for investments,
- Sorting of foams for better recycling,
- Recycling all foam components,
- Harmonization of (End-of-life) legislation,
- Recycled content certification.
You can find more details about specific challenges by reading this brochure.
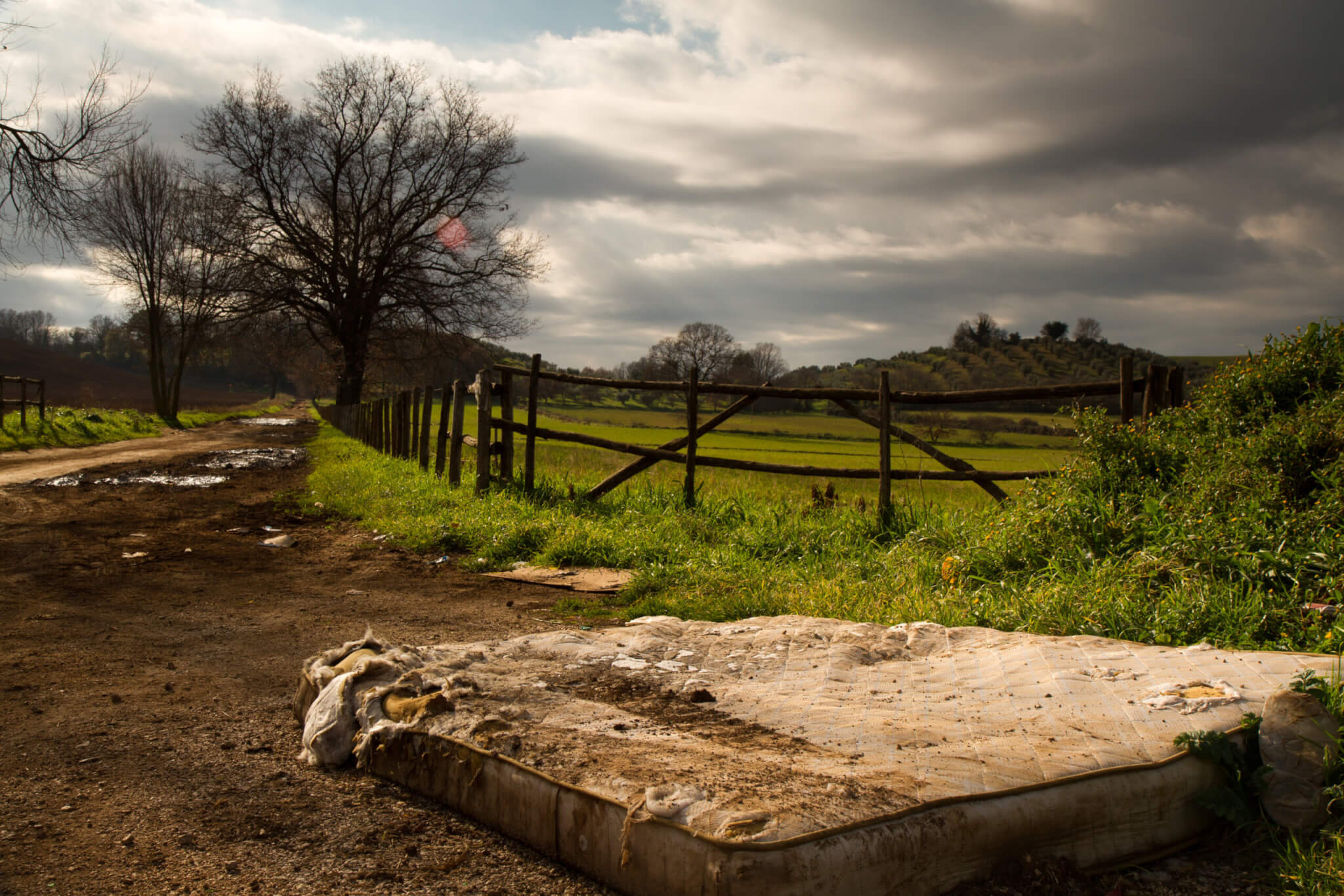